Protecting employees and ensuring health and safety at work (HSW), especially in operations where there is a greater risk of workplace accidents and occupational diseases, is a constant concern. To this end, we fully comply with the applicable laws and have an HSW management system in place, which includes good practices in risk assessment and management, as well as in workplace accidents and occupational diseases management.
We have implemented policies, processes and procedures to prevent and mitigate risks and that guide the actions of our teams. In this regard, we carry out audits, drills and regular consultations and health assessments, making teams aware of the dangers and of safe practices through training and employee engagement. Also of note is the regular monitoring of the major HSW indicators:
Rate of accidents of mandatory reporting
Rate of workplace accidents of mandatory reporting = (Number of workplace accidents that must be reported/Total hours worked) x 106. Workers that are not employees of the Group are not included.
Rate of accidents with serious consequences
Rate of workplace accidents with serious consequences (except deaths) = (Number of workplace accidents with serious consequences (except deaths)/Total hours worked) x 106. Accidents with serious consequences are those that result in an employee being absent for more than 180 days. Workers that are not employees of the Group are not included.
In 2023 there were 4.9% fewer workplace accidents of mandatory reporting in Portugal, thanks to the Companies’ investment in initiatives that promote safe working conditions and create an environment of prevention and care. However, due to the number of store openings and refurbishments and the turnover of workers who are not employees, Poland saw a slight increase in the number of workplace accidents. The inclusion of a new cause of accidents related to muscular overexertion from handling loads also resulted in a slight increase in workplace accidents in Colombia. As a result, there was a 4.8% increase in the rate of accidents of mandatory reporting. The rate of accidents with serious consequences remained stable at 0.16.
Risk identification and assessment
To create and maintain an increasingly safe and healthy working environment, we are committed to implementing risk identification and assessment systems that include the definition and implementation of risk control and mitigation measures.
To identify and assess risks, HSW technicians conduct an assessment that allows them to quantify the magnitude of existing risks and thus prioritise the elimination and/or mitigation of those risks. This assessment is carried out based on a risk matrix applied to all areas and processes, which is used to describe the risks, their causes and potential effects, the degree of exposure, severity and risk, and recommends the most appropriate measures to address them.
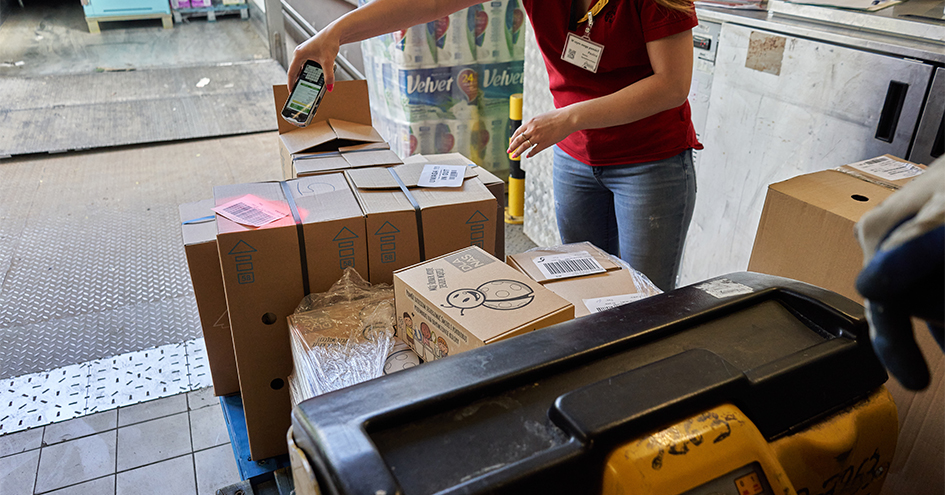
The identified risks can be classified into seven categories: environmental (physical, chemical and biological), mechanical, electrical, fire and/or explosion, ergonomic, psychosocial and organisational. Given that food distribution is our most relevant business area, there are activities that could pose additional risks to employees, in particular those who work in warehouses, industrial kitchens and stores, and who load/unload and store products and process them (e.g., fish and meat cutting, bread making, and meal preparation). Jerónimo Martins Agro-Alimentar employees work in the primary and secondary sectors and are also exposed to specific risk factors1.
The results obtained by identifying and assessing risks inform the selection of work equipment and tools, the preparation of work procedures and instructions, the structuring of training content, and the definition of action plans for continuous improvement of the HSW management system.
Risk control measures
Work and personal protective equipment
Whenever the need to install new work equipment is identified, the safety requirements are defined in advance and checked after installation. Work instructions are drawn up that include safety, handling, maintenance and cleaning actions, being provided to employees. The equipment manufacturer/representative also trains the teams. The need to use personal protective equipment (PPE) is also identified in the risk assessment and selection is based on user tests and a technical assessment.
In Portugal, based on the feedback from 13,917 employees through a dedicated survey on workplace footwear, we replaced around 29 thousand pairs of shoes used by employees, also taking into account specific orthopaedic and anatomical needs, with custom-made footwear. A total of 543 thousand euros were invested in this measure. JMA invested a total of 230 thousand euros in renewing its safety and preventive equipment, including containment basins, emergency showers, fuel tank covers, safety belts, anti-slip covers, and forklifts.
In Poland, Hebe replaced its entire fleet of forklifts and the packing crates used in its stores and distribution centre, reducing their maximum weight capacity to better protect the physical integrity of employees.
Self-protection measures
To test effectiveness, the Companies provide and regularly implement self-protection measures that include safety records, emergency plans, and prevention plans and procedures.
In Portugal, with Segurança Máxima (Maximum Safety) and Segurança em Ação (Safety in Action) programmes, Pingo Doce and Recheio, respectively, involved their store teams in practising safe behaviours on an ongoing basis in their day-to-day operations. These programmes are preventative in nature and involve close monitoring and immediate intervention, where behaviour that could potentially result in a workplace accident is identified.
In Colombia, Mi CEDI Seguro (My Safe Distribution Centre) programme comprises preventive measures such as daily inspections of equipment and racks, monthly safety observations, warm-up exercises for each shift, and training for new employees. The programme also includes emergency brigades, made up of 289 employees identified and certified to lead drills and other HSW initiatives, and provide assistance in the event of an emergency. The programme also includes mapping the HSW competencies of distribution centre employees and the design of training plans based on the results of this assessment. In 2023, a total of 152 employees were mapped. Ara’s commitment to safety and self-care is embodied, for example, in the Cúcuta Distribution Centre reaching the milestone of 737 accident-free days in 2023, a Company record. Ara also has 413 HSW leaders identified and trained in safe behaviours and the Atento observation tool.
Health
We have doctors specialised in occupational health who visit different workplace to assess the health impacts on our people and prescribe corrective actions, as well as to carry out medical fitness tests.
In Portugal, we introduced two mobile health units to increase the frequency of medical assessments, ensuring that employees are fit to work, and to treat and prevent illnesses and injuries associated with each job. These units are vehicles that have been converted into fully-equipped doctors’ offices that complement the in-house consultation rooms in some workplaces and travel around the country. These mobile units assisted 3,196 employees in 2023.
In 2023, fewer occupational health exams were carried out, explained by the fact that in 2020 and 2021, at the height of the pandemic, some assessments were suspended, which meant that 2022 was a year of recovery. In 2023, there was a return to normalcy in occupational health exams.
|
|
Occupational health exams |
||||
---|---|---|---|---|---|---|
|
|
2023 |
|
2022 |
|
2021 |
Group |
|
136,620 |
|
141,451 |
|
125,769 |
Portugal |
|
36,468 |
|
33,914 |
|
30,878 |
Poland |
|
83,514 |
|
92,782 |
|
86,302 |
Colombia |
|
16,638 |
|
14,755 |
|
8,589 |
Training and awareness-raising
To promote prevention and the practice of safe behaviours, the general training plan and its contents are reviewed annually. Training is provided at different points in an employee’s career, such as when they are hired, when they change jobs, when new equipment is introduced or when existing equipment is modified. Based on their role and the risks associated with it, employees are also given access to pre-defined training courses.
In Poland, most noteworthy is the Biedronkowa Akademia Zdrowia (Biedronka Health Academy), which focuses on the prevention of occupational diseases. It offers health and safety training by physiotherapists who teach employees how to prevent musculoskeletal problems, as well as physiotherapy appointments and daily warm-up exercises. In 2023, a total of 2,886 employees were trained and 31,986 consultations provided (20.7% more than in 2022). The Company also has a prevention programme that includes education campaigns and training on the most common causes of workplace accidents and how to reduce them, which reached 79,268 employees.
Hebe has a channel on the internal EducAction platform dedicated to raising awareness of HSW issues, where it uploads short videos on accident prevention, safe behaviour and safety instructions. First-aid training was also provided to store employees through videos that garnered 1,441 views, and to employees who use a company car.
In Portugal, the Impacto Programme was created, consisting of a series of training sessions organised by the Companies’ safety technicians. In 5,096 hours of training, 728 safety delegates learned how to motivate the teams they work with to adopt safe behaviours and cultivate a self-care approach.
|
|
Employees trained in HSW |
|
HSW training volume (i) |
||||||||||||||
---|---|---|---|---|---|---|---|---|---|---|---|---|---|---|---|---|---|---|
|
|
2023 |
|
2022 |
|
2021 |
|
2023 |
|
2022 |
|
2021 |
||||||
Group |
|
63,221 |
|
76,875 |
|
60,785 |
|
388,831 |
|
444,494 |
|
337,079 |
||||||
Portugal |
|
23,109 |
|
25,192 |
|
22,400 |
|
72,062 |
|
74,902 |
|
62,034 |
||||||
Poland |
|
30,807 |
|
40,133 |
|
33,277 |
|
274,655 |
|
335,216 |
|
240,266 |
||||||
Colombia |
|
9,305 |
|
11,550 |
|
5,108 |
|
42,115 |
|
34,376 |
|
34,779 |
||||||
|
Continuous improvement of the health and safety at work management system
The verification and review of our HSW management system enables us to confirm the implementation and effectiveness of risk control measures, with a view to continuous improvement.
Audits – a systematic approach for identifying and analysing the factors that can lead to incidents/accidents, monitoring the remedy mechanisms, communicating the outcomes to stakeholders, and designing and following up on action plans until they are completed;
Drills – periodic confirmation of the adoption of self-protection measures in order to identify potential deficiencies and increase emergency response capacity, by structuring and monitoring a corrective action plan.
|
|
Audits |
|
Drills |
||||||||
---|---|---|---|---|---|---|---|---|---|---|---|---|
|
|
2023 |
|
2022 |
|
2021 |
|
2023 |
|
2022 |
|
2021 |
Group |
|
11,002 |
|
9,661 |
|
9,625 |
|
4,797 |
|
4,129 |
|
3,330 |
Portugal |
|
601 |
|
570 |
|
567 |
|
262 |
|
277 |
|
265 |
Poland |
|
9,121 |
|
8,127 |
|
8,297 |
|
3,252 |
|
2,908 |
|
2,231 |
Colombia |
|
1,280 |
|
964 |
|
761 |
|
1,283 |
|
944 |
|
834 |
Accident investigation – reporting and describing the facts, including the logical sequence of events, determining the root cause, identifying contributing factors, identifying shortcomings in the HSW management system, and designing, monitoring and reporting on the corrective action plan.
Employee consultation and involvement – our Companies have different mechanisms for listening to their employees’ concerns on HSW issues. In Portugal, employees are invited to share their opinion in two HSW surveys each year. Biedronka has an HSW Committee, which meets every month and is attended by employee representatives. It also has 17 regional teams responsible for implementing and maintaining the HSW system. At Hebe, an HSW Committee, comprising representatives of the Company’s management and employees, holds quarterly meetings. In Colombia, the HSW Committee raises awareness about situations that may harm the health and safety of employees.
Certification of HSW management systems – certification of HSW systems enables alignment with international quality requirements and standards and guidance for continuous improvement in our approach to HSW. At Biedronka, the system is certified to ISO 45001:2018, covering all 3,369 workplaces (stores, distribution centres, soup factory and offices), with 1,453 new instructions for improving team protection implemented over the course of the year. In Portugal, the Terra Alegre dairy factory has its HSW management system certified to ISO 45001:2019. In both cases, certification covers employees and workers who are not employees.
1 The occupational hazards at these workplaces and of the tasks performed there include, among others, exposure to extreme temperatures, with possible vascular injuries, physical exertion, with possible musculoskeletal injuries, and contact with machinery, with possible traumas, wounds and electrocution.