Having a Health and Safety at Work (HSW) management system in place is essential to our commitment to ensuring that our employees are protected, especially in store and logistics operations, where they are exposed to a greater risk of work-related accidents and work-related ill health. In 2024, 100% of the Group’s workforce was covered by a HSW management system.
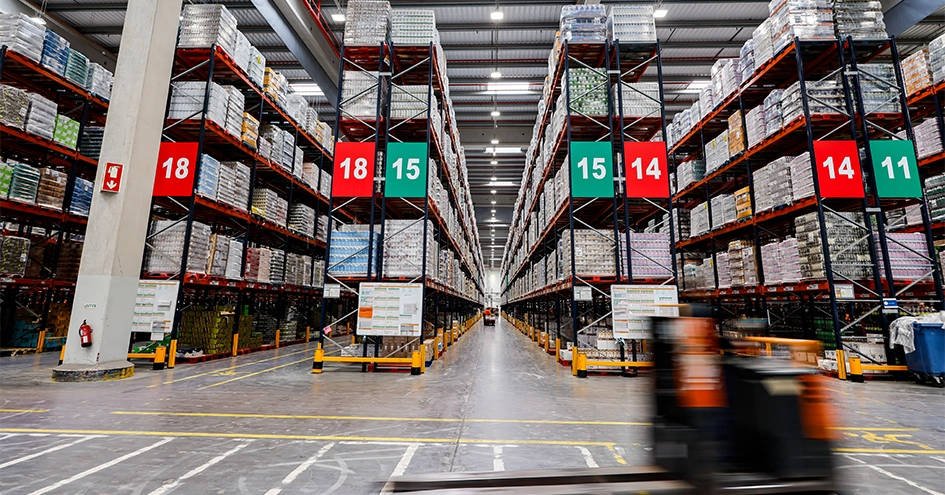
We therefore have formal policies, processes and procedures that guide the actions of our teams in risk assessment and management, accident and occupational ill health management, audits and drills, as well as training and awareness-raising activities for the adoption of safe behaviours.
Key incident indicators
Employees |
|
|
||||||
---|---|---|---|---|---|---|---|---|
Number of fatalities |
|
1 |
||||||
Number of high-consequence work-related injuries |
|
49 |
||||||
Number of recordable work-related injuries |
|
4,300 |
||||||
Hours worked |
|
219,831,048 |
||||||
Rate of high-consequence work-related injuries1 |
|
0.22 |
||||||
Rate of recordable work-related injuries2 |
|
19.56 |
||||||
Number of days lost due to injuries |
|
2,609 |
||||||
Workers who are not employees |
|
|
||||||
Number of fatalities |
|
2 |
||||||
Number of high-consequence work-related injuries |
|
0 |
||||||
Number of recordable work-related injuries |
|
219 |
||||||
|
In 2024 there were 4,300 recordable work-related injuries, 12.7% less than in the same period last year, of which 49 were of high consequences, resulting in a rate of recordable work-related injuries of 19.56 (16.0% lower than the rate of 23.29 registered in 2023) and a rate of high-consequence work-related injuries of 0.22 (38.7% higher than the previous year, which stood at 0.16). In the case of workers who are not employees, there were 219 recordable work-related injuries. In addition, there was one fatality of a Pingo Doce employee and two fatalities of workers who are not employees.
Employees |
|
|
||||
---|---|---|---|---|---|---|
Number of fatalities |
|
0 |
||||
Number of cases of recordable work-related ill health |
|
117 |
||||
Workers who are not employees1 |
|
|
||||
Number of fatalities |
|
0 |
||||
Number of cases of recordable work-related ill health |
|
7 |
||||
|
In 2024, 117 cases of recordable work-related illnesses were recorded, which corresponds to an increase of 11.4% compared to the same period last year.
Risk identification and assessment
Our local HSW teams are tasked with identifying risks and assessing them in order to eliminate or minimise existing work-related risks. Assessments are carried out using a method that enables us to quantify the magnitude of the existing risks and thus prioritise them according to a risk matrix. The matrix covers all areas and processes assessed, and includes the collection of information about the circumstances, causes, effects, levels of exposure, severity and risk, and the most appropriate remedy/recommendation. A new methodology for risk identification and assessment is currently being implemented to ensure alignment with the ISO 45001:2024 standard.
There are seven different types of risks:
- environmental (physical, chemical and biological);
- mechanical;
- electrical;
- fire and/or explosion;
- ergonomic;
- psychosocial;
- organisational.
As food distribution accounts for over 98% of our sales, there are activities that could pose risks to employees who, in warehouses, industrial kitchens and stores, deal with the loading/unloading and storage of products and their processing (e.g. fish and meat cutting, bread making, and meals preparation). Jerónimo Martins Agro-Alimentar employees work in the primary and secondary sectors and are also exposed to specific risk factors, such as unfavourable thermal environments, with possible vascular injuries, physical exertion, with possible musculoskeletal injuries, and contact with machinery, with possible trauma, wounds and electrocutions.
Risk assessment and the respective findings are key to identifying and selecting work equipment and tools, preparing procedures and work instructions, planning training content and individual protection measures, and for defining initiatives that promote the continuous improvement of the HSW management system.
Risk control measures
Work and personal protective equipment
Work-related risks require the selection of appropriate work and personal protective equipment. Whenever the need to install new work equipment is identified, the safety requirements are defined in advance and checked after installation. Work instructions are drawn up that include safety, handling, maintenance and cleaning actions, and are provided to employees. The equipment manufacturer/representative also trains the teams. The need to use personal protective equipment (PPE) is also identified in the risk assessment and selection is based on user tests and a technical assessment.
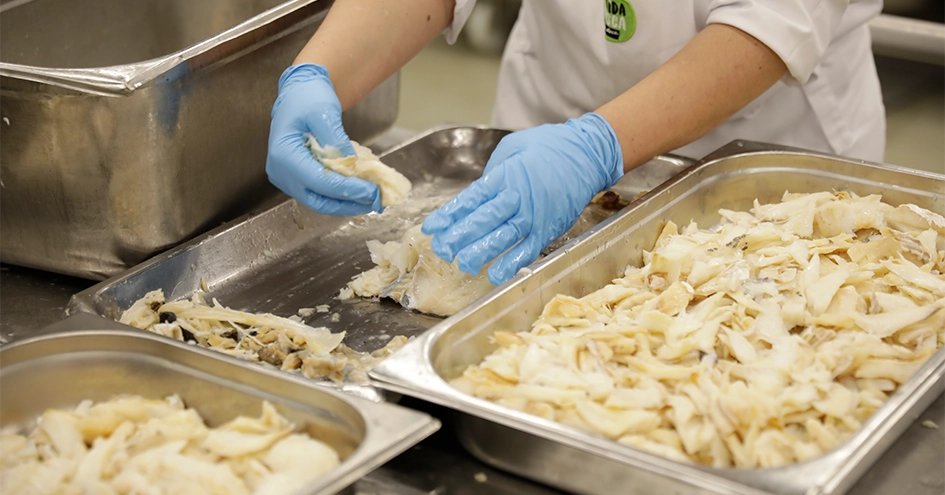
The Companies continually evaluate the need to replace equipment and test it regularly to prevent work-related accidents and work-related ill health. In 2024, for instance, and to improve safety, productivity and employee wellbeing, Pingo Doce rearranged the fish counter in 64 stores, investing over 920,000 euros. JMA continued to invest in the renewal of safety equipment, with the purchase of gas detectors in confined spaces, fire cabinets, individual diving computers and flotation devices standing out in 2024, in an investment of 67,000 euros.
Self-protection measures
Companies provide and periodically put into practice – with the aim of testing their effectiveness – self-protection measures that include safety records, emergency plans and prevention plans and procedures.
In Portugal, the programmes “Segurança Assim Sabe Tão Bem” (It’s Good to Feel Safe), which replaces the former “Segurança Máxima” (Maximum Safety) programme, from Pingo Doce, and “Segurança em Ação” (Safety in Action) from Recheio, encourage store teams to adopt safe behaviours throughout their day-to-day operations. These programmes are preventive and involve close monitoring and immediate intervention, when behaviours that could potentially result in a work-related accident are identified.
Ara’s “Mi CEDI Seguro” (My Safe Distribution Centre) programme includes several preventive measures such as daily inspections of equipment and racks, monthly safety observations, warm-up exercises before each shift, and training for new employees, with the support of emergency brigades (employees certified to conduct drills, support safety initiatives and provide assistance in emergency situations). HSW skill assessments are also carried out and training plans drawn up based on the findings. Based on the safety metrics assessed, and to encourage employees to adopt safe behaviours, the Company recognises the distribution centres with the best HSW performance and rewards them with leisure and wellbeing measures. Ara also has 380 HSW leaders trained to observe and promote safe behaviours.
Training and awareness-raising
We believe it is equally important to invest in making employees aware of the risks inherent in their jobs and the importance of adopting good practices through training. The general training plan and the contents thereof are reviewed each year and training is provided at different points in an employee’s career, such as when they are hired, when they change jobs, when new equipment or tools are introduced or when existing ones are modified. Based on their role and the risks associated with it, employees are also given access to pre-defined training courses.
The Impact Programme, created in 2023 for all Group Companies in Portugal, has two components, with a total of 676 participants and a total of 4,732 hours of training:
- Laboratórios de Segurança (Safety Labs), with training sessions led by the Company’s safety technicians to teach safety delegates how to encourage the teams they work with to adopt safe behaviours and cultivate a self-care approach;
- Liderança com Impacto (Leadership with Impact), an initiative launched in 2024 specifically for operations managers (stores, logistics and central kitchens), given their role in transforming team behaviours, demonstrating that humanised leadership can more easily influence employees to adopt safe behaviours, thus preventing work-related accidents and work-related ill health.
At Biedronka, of note is the “Biedronkowa Akademia Zdrowia” (Biedronka Health Academy), focusing on preventing work-related ill health through health and safety training sessions led by physiotherapists who teach employees how to prevent musculoskeletal injuries, including physiotherapy appointments and daily warm-up exercises. In 2024, 3,322 employees were trained and 30,243 appointments facilitated.
|
|
Employees trained in HSW |
|
HSW training volume1 |
||||||||||||
---|---|---|---|---|---|---|---|---|---|---|---|---|---|---|---|---|
|
|
2024 |
|
2023 |
|
2022 |
|
2024 |
|
2023 |
|
2022 |
||||
Group |
|
74,267 |
|
63,221 |
|
76,875 |
|
430,181 |
|
388,831 |
|
444,494 |
||||
Portugal |
|
25,779 |
|
23,109 |
|
25,192 |
|
72,723 |
|
72,062 |
|
74,902 |
||||
Poland |
|
35,871 |
|
30,807 |
|
40,133 |
|
311,650 |
|
274,655 |
|
335,216 |
||||
Colombia |
|
12,486 |
|
9,305 |
|
11,550 |
|
44,176 |
|
42,114 |
|
34,376 |
||||
Slovakia |
|
131 |
|
– |
|
– |
|
1,632 |
|
– |
|
– |
||||
|
Health
We have doctors who specialise in occupational health who visit different workplaces to assess health impacts on our people and prescribe corrective actions, and to carry out medical fitness tests.
We carry out health assessments at the start of employment, as well as regular and periodic examinations to monitor employees’ health throughout their professional lives and to assess their physical and mental fitness. In 2024, we carried out 137,064 occupational health assessments.
In Portugal, our two mobile health units help increase the frequency of health assessments, thus ensuring that employees are fit to work, and to treat and prevent illnesses and injuries associated with each function. These units are vehicles that have been converted into fully-equipped medical offices that complement the in-house consultation rooms in some workplaces and travel around the country. These mobile units assisted 4,366 employees in 2024.
Continuous improvement of the health and safety at work management system
We strive to ensure the continuous development and improvement of our HSW management systems, performing audits and drills, investigating accidents/incidents, and consulting and involving our employees in decision-making.
Audits – assessment and analysis of the factors that can lead to accidents/incidents, monitoring the remedy mechanisms, communicating the outcomes to stakeholders, and designing and following up on action plans until they are completed.
Drills – regular and controlled drills to test self-protection procedures in order to identify potential deficiencies and minimise the risk of mistakes in emergency response, by structuring and monitoring a corrective action plan.
|
|
Audits |
|
Drills |
||||||||
---|---|---|---|---|---|---|---|---|---|---|---|---|
|
|
2024 |
|
2023 |
|
2022 |
|
2024 |
|
2023 |
|
2022 |
Group |
|
9,765 |
|
11,002 |
|
9,661 |
|
5,244 |
|
4,797 |
|
4,129 |
Portugal |
|
599 |
|
601 |
|
570 |
|
270 |
|
262 |
|
277 |
Poland |
|
7,789 |
|
9,121 |
|
8,127 |
|
3,645 |
|
3,252 |
|
2,908 |
Colombia |
|
1,377 |
|
1,280 |
|
964 |
|
1,329 |
|
1,283 |
|
944 |
Accident investigation – assessments and investigations are carried out after an incident has been reported to ascertain the facts, circumstances and possible causes, and to design, monitor and report on corrective action plans implemented to prevent it from happening again.
Employee consultation and engagement – in Portugal, employees are invited to share their opinion in two HSW surveys each year. In Poland, both Biedronka and Hebe have an HSW Committee that meets regularly, comprising employee representatives and representatives of the HSW teams. Biedronka also has 17 regional teams responsible for implementing and maintaining the HSW system. In Colombia, the HSW Committee raises awareness about situations that may harm the health and safety of employees.
Certification of HSW management systems – certification of HSW systems promotes the principle of continuous improvement in workplace health and safety practices, ensuring alignment with international best practices. At Biedronka, the system is certified to ISO 45001:2018, covering all 3,778 workplaces (stores, distribution centres, soup factory and offices), and a total of 1,447 new work instructions were implemented to improve team protection. In Portugal, the Terra Alegre dairy factory (JMA) has its HSW management system certified to ISO 45001:2019. The two Meal Solutions central kitchens (Pingo Doce) are ISO 45001:2023 certified. In all cases, certification covers employees and workers who are not employee.
Certification of HSW management systems in Biedronka, Terra Alegre and Meal Solutions kitchens (Pingo Doce) |
|
Total |
|
% |
---|---|---|---|---|
Employees and workers who are not employees covered by the HSW system |
|
102,051 |
|
100 |
Employees and workers who are not employees covered by the internally audited HSW system |
|
102,051 |
|
100 |
Employees and workers who are not employees covered by the externally audited HSW system |
|
24,839 |
|
24.3 |