Social criteria related to labour aspects1 are included in our food safety and quality supplier selection audits, as described above. Social aspects are further complemented in our regular social audits of perishables and Private Brand suppliers from whom we make purchases of more than one million euros per year.
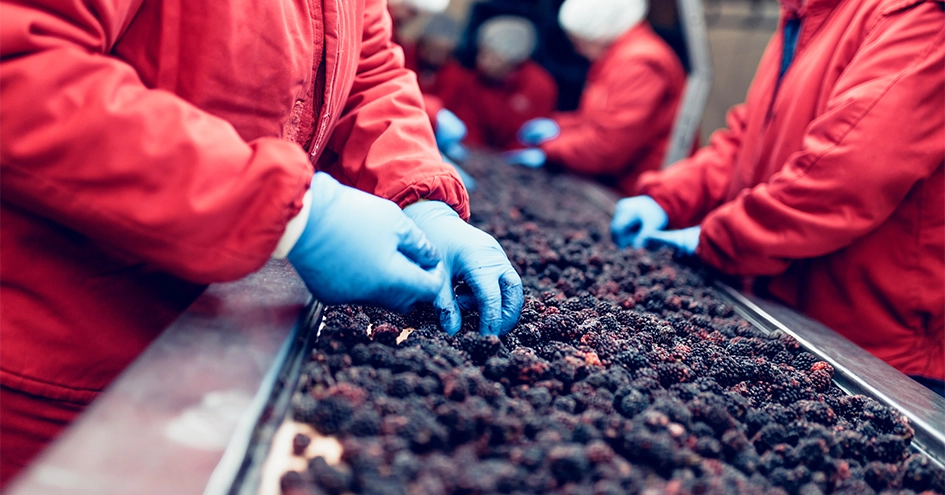
Our social audit programme allows our Companies to carry out due diligence to assess supplier’s procedures, while preventing and mitigating potential human and labour rights risks, in line with the principles of our Sustainable Sourcing Policy. The programme also allows our partners to gain a better understanding of social issues, minimise risks and ultimately increase their capacity to expand to other countries with more demanding labour requirements.
These audits, carried out by an external and independent entity, are preceded by an explanatory session with our partners, which analyses compliance with national and international laws and considers the best practices shared by The Consumer Goods Forum’s Sustainable Supply Chain Initiative. There are three audit schemes aimed at incorporating aspects related to high-risk sectors: primary production, operations at sea and the manufacturing industry.
Social audits assess over 125 requirements across the following 12 dimensions: prevention of child labour, prevention of forced labour, prevention of discrimination, safeguarding the right of association, contractual terms, working hours, wages and benefits, health and safety at work, emergency preparedness, compliance monitoring, business ethics, and protection of human rights, including criteria we consider to be of “zero tolerance”.
In addition to the document analysis provided by management and on-site inspections, interviews are carried out with employees in the value chain to triangulate the information. In all audits, a sample representing the average global workforce of the audited company as well as workers from vulnerable groups (such as migrants and under temporary contracts) are interviewed, as well as employees who, during the visit, were deemed as being at social risk.
The interviews are conducted considering the worker’s specific circumstances and observations made during the visit. The interview always respects the principles of confidentiality and non-retaliation. Additional information on these processes is described in “Workers in the value chain”.
Based on the overall score obtained, we have defined five levels of compliance2: Excellent, Very Good, Good, Satisfactory and Inadequate.
Overall Performance of Social Audits of Perishables, Private Brand and Exclusive Brand Suppliers
In 2024 in-person audits were carried out at 19 direct suppliers. These audits were also based on the suppliers’ social risk, as identified in the List of Goods Produced by Child Labor or Forced Labor, per Country, developed by the Bureau of International Labor Affairs (ILAB). Local suppliers in Portugal and Colombia were audited. Eight suppliers classified as “Inadequate” in previous cycles were re-audited and four of them were re-evaluated as “Excellent”. The remaining four maintained an “Inadequate” score.
A personalised corrective action plan was presented to and discussed with all suppliers, where the assessment had identified critical non-conformities requiring a mandatory response within 12 months at the most, depending on the level of severity. During this 12-month period, additional contact is established with the supplier to review progress in the implementation of the plan.
Suppliers with a score of “Inadequate” are regularly contacted to confirm implementation of the corrective action plan. An in loco or remote assessment is performed the following year for further evaluation. If there is no evidence of progress, we reserve the right to suspend the business relationship, as defined in our Sustainable Sourcing Policy.
1 Labour related aspects, which account for 10% of the assessment, are related to the quality and safety of products. These audits assess elements such as health and safety working conditions, training, the use of appropriate clothing, hand washing equipment, rules of conduct and personal hygiene, the existence of adequate social areas, changing rooms, and employee bathrooms.
2 The results of each supplier are measured based on full or partial compliance or non-compliance with critical requirements, general-level requirements and, where applicable, good practice requirements. The five levels of compliance are: (i) Excellent: compliance with 100% of the critical requirements and compliance with at least 95% of the general-level and good practice requirements; (ii) Very Good: 100% compliance with the critical requirements and compliance with between 85% and 94% of the general-level and good practice requirements; (iii) Good: Compliance with 100% of the critical requirements and compliance with between 75% and 84% of the general-level and good practice requirements; (iv) Satisfactory: Compliance with 100% of the critical requirements and compliance with between 65% and 74% of the general-level and good practice requirements; (v) Inadequate: non-compliance, albeit partial, with at least one critical requirement and/or compliance with less than 65% of the general-level and good practice requirements.