Continued investment in the certification and supervising of our processes, facilities and equipment, as well as monitoring the upstream production activities of our supply chain, are the foundations of the reputation capital of our banners and businesses. To preserve this, we recognise our responsibility to prevent and mitigate negative impacts while promoting a safe customer experience in our stores and through our products. To that end, we rely on a set of different actions, including:
- risk assessments and Companies’ certifications;
- internal audits of stores and distribution centres;
- facility analyses;
- product analyses;
- product recalls and withdrawals;
- food hygiene and safety internal training.
Our cooperation with thousands of suppliers that produce our perishable and Private Brand products is carried out through rigorous assessments (including monitoring corrections to their procedures if needed) to ensure that products are safe for consumption. Please see “Selection and monitoring of suppliers” for more information about audits in the supply chain.
We believe that by promoting quality as an integral concept, our Companies not only contribute to the competitiveness and sustainable development of our business and our suppliers, but also generate consumer trust and improve the quality of life of the millions of customers who choose our stores every day.
In 2024, we carried out 18,219 internal audits of our infrastructures (8% more than in 2023), 252,851 facility analyses (3% less) and 89,832 analyses on food products (10% more).
Risk assessments and certifications
The risk assessments made for our Private Brand products and perishables are carried out by our quality and product development teams and take into consideration factors such as:
- laws in force and the technical specifications issued by the official authorities;
- recommendations of the European Union and/or other official bodies;
- the Rapid Alert System for Food and Feed (RASFF) urgent notifications and known food fraud incidents;
- physical characteristics of products (such as perishability) and organoleptic properties (such as colour, texture, taste or smell);
- country of origin of production and/or supply of the products and the track record of trade partners;
- market expansion (stores and distribution centres);
- surrounding conditions (sanitation or weather conditions related to humidity and average temperatures);
- opting for facility certification schemes;
- results of past assessments.
Certification plays an important role in setting high quality and safety standards for our Companies’ facilities, as it fosters a more integrated management approach for a business that comprises millions of products flowing through thousands of stores, while continuously contributing towards improving our procedures.
During 2024, the following certifications were renewed or extended to new facilities:
- ISO 22000:2018 at 17 Biedronka distribution centres for the storage and distribution of food products and at the Biedronka head office for the development of Private Brand food products.
- FSSC 22000 v.6.0 (which includes ISO 22000:2018) for the soup factory in Poland, with regard to ready-to-eat after heating and individualised packaging;
- ISO 9001 for the development of Private Brands in Portugal and post-launch product/supplier follow-up;
- HACCP1 in accordance with the Codex Alimentarius2 for the two Pingo Doce central kitchens (with regard to food safety), 11 Recheio stores (two less than in 2023, explained by the transition of these and the Recheio MasterChef food service platform in Lisbon to the ISO22000 certification process shown below), and for all seven distribution centres in Portugal (with regard to food safety);
- Food Safety Management System, according to the EN ISO 22000:2018 Portuguese Standard, in 28 Recheio stores (two more vs. 2023) and three Recheio MasterChef food service platforms (one more vs. 2023);
- Organic product handling certification, in accordance with Council Regulation (EC) No 848/2018, was renewed in Poland for the 18 distribution centres. All our four distribution centres in Portugal that handle organic products hold this certification;
- Certification of 486 Biedronka stores regarding the correct storage and preparation of organic products.
We also work with external auditors (independent and accredited laboratories) and have our own molecular biology laboratory, all of which contribute to an even safer and higher quality delivery to consumers. The Jerónimo Martins laboratory, located in Portugal, complements the verification made during the product development and supply processes and focuses on the authenticity of the ingredients in our products, from all Companies. It is accredited according to the NP EN ISO/IEC 17025:2018 Portuguese Standard (Instituto Português de Acreditação e Certificação – IPAC – is the certifying entity), a framework that sets laboratories’ general competence requirements for testing and calibration. In 2024, over 6,900 Next-Generation DNA Sequencing (NGS) tests were made to molluscs, crustaceans, meat, fish and GMO screening.
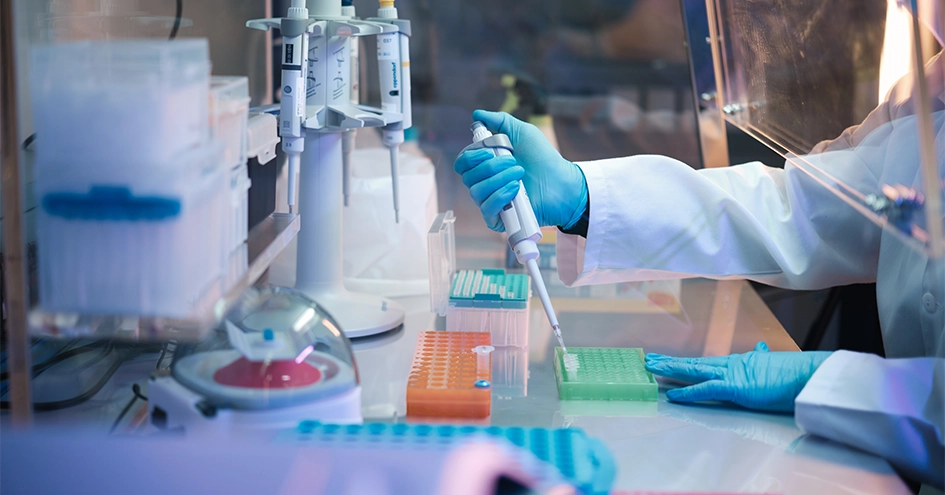
Internal audits to stores and distribution centres
With specialised internal and, when applicable, external product safety and quality teams, and in accordance with the business unit and infrastructure to be assessed, internal audits are conducted by considering criteria arranged into dimensions such as basic hygiene conditions, cleanliness and disinfection, facility and equipment maintenance, good production practices, product handling, water availability, metrology, pest control, waste management, records, traceability, and procedure review.
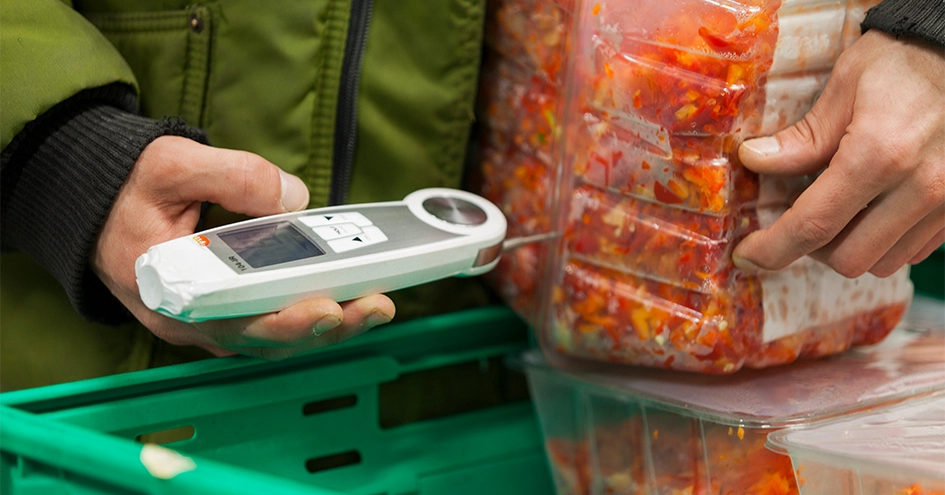
These audits assign scores with specific levels to the business units (according to country and infrastructures, these can range from Inadequate, Basic, Satisfactory, to Good, Very Good or Excellent), and the potential corrective actions to be taken are made to any non-conformities identified. The timeframe to mitigate and remedy the identified issues may vary from immediate resolution to a subsequent audit.
Poland
Biedronka stores and distribution centres were audited by both internal and external auditors to check facilities, equipment and procedures.
|
|
Stores |
|
Distribution centres |
||||||||||||
---|---|---|---|---|---|---|---|---|---|---|---|---|---|---|---|---|
Biedronka |
|
2024 |
|
2023 |
|
Δ 2024/2023 |
|
2024 |
|
2023 |
|
Δ 2024/2023 |
||||
Internal audits |
|
9,657 |
|
8,687 |
|
+11.2% |
|
36 |
|
38 |
|
-5.3% |
||||
Follow-up audits |
|
172 |
|
248 |
|
-30.6% |
|
– |
|
– |
|
– |
||||
External audits |
|
38 |
|
34 |
|
+11.8% |
|
23 |
|
9 |
|
+155.6% |
||||
HACCP Performance1 |
|
87% |
|
84% |
|
+3 p.p. |
|
91% |
|
88% |
|
+3 p.p. |
||||
|
More internal audits of the stores were carried out as a result of Biedronka’s expansion (161 more stores than in 2023), of the increase in the number of meat counters (23% more compared to 2023)3, and the growth of the number of micro-fulfilment centres for the Biek operation4. The decrease in follow-up audits is due to the classification of the stores in the previous audits, which – because of its good results – led to a reduction in the frequency of monitoring.
Despite the fact that Biedronka adjusted the number of stores selling organic bread that were subject to external auditing, with three less stores than the previous year (-0.6%)5, the number of external controls imposed by responsible authorities has led to an overall increase.
At distribution centres, the number of internal audits decreased slightly as a result of risk assessment – previous audits were carried out in 2023, making it no longer necessary to perform the same number of audits in 2024. The good audits’ results that have been registered year-on-year have allowed for a reduction on the number of follow-up audits, which were therefore replaced by our standard internal audit procedure: a minimum of two audits per year, per location. The increase in external audits is explained by our compliance with the ISO22000 certification. In 2024, all audits happened at the beginning of the year, while in 2023 audits occurred even earlier, at the end of 20226.
Portugal
|
|
Pingo Doce stores |
|
Recheio stores |
|
Distribution centres2 |
||||||||||||||||||
---|---|---|---|---|---|---|---|---|---|---|---|---|---|---|---|---|---|---|---|---|---|---|---|---|
|
|
2024 |
|
2023 |
|
Δ ‘24/’23 |
|
2024 |
|
2023 |
|
Δ ‘24/’23 |
|
2024 |
|
2023 |
|
Δ ‘24/’23 |
||||||
Internal audits |
|
486 |
|
485 |
|
+0.2% |
|
86 |
|
99 |
|
-13.1% |
|
38 |
|
31 |
|
+22.6% |
||||||
Follow-up audits |
|
3,006 |
|
2,886 |
|
+4.2% |
|
365 |
|
246 |
|
+48.4% |
|
235 |
|
196 |
|
+19.9% |
||||||
External audits |
|
91 |
|
74 |
|
+23.0% |
|
18 |
|
21 |
|
-14.3% |
|
9 |
|
7 |
|
+28.6% |
||||||
HACCP Performance1 |
|
88% |
|
87% |
|
+1 p.p. |
|
87% |
|
84% |
|
+3 p.p. |
|
77% |
|
84% |
|
-7 p.p. |
||||||
|
At Pingo Doce, despite the opening of ten additional stores in 2024 (bringing the total network to 489 locations), the number of audits slightly increased since priority was given to following-up on the stores identified as needing improvement in 2023. For the second year, this method has led to an increase in its HACCP performance, adding to the increase of 5 p.p. in 2023 versus 2022.
The number of Recheio stores in 2024 remained unchanged at 43. Nevertheless, the decrease in the number of internal audits is due to the risk matrix and prioritisation used by the operational food safety teams, that in 2024 have given priority to monitoring the correction of identified non-conformities in the previous year. The Company has increased its HACCP performance.
In the distribution centres, where audits also cover the central kitchens and internal canteens, the increase in internal and follow-up audits – registered since 2023 – is the result of a greater sampling, with three more distribution centres covered by the HACCP certification requirements, and continuous monitoring by a dedicated team. This led to a decrease in the associated performance, as more opportunities for improvement were identified.
In Pingo Doce, Recheio and in distribution centres, external audits are carried out by the local authorities according to their own planning.
Colombia
Audits to Ara stores were carried out by an independent entity (Diversey). Our internal quality teams carried out the audits on the distribution centres.
|
|
Stores |
|
Distribution centres |
||||||||||||
---|---|---|---|---|---|---|---|---|---|---|---|---|---|---|---|---|
Ara |
|
2024 |
|
2023 |
|
Δ 2024/2023 |
|
2024 |
|
2023 |
|
Δ 2024/2023 |
||||
Internal audits |
|
2,715 |
|
2,422 |
|
+12.1% |
|
12 |
|
10 |
|
+20.0% |
||||
Follow-up audits |
|
1,402 |
|
1,513 |
|
-7.3% |
|
9 |
|
8 |
|
+12.5% |
||||
Good hygiene and quality practices1 |
|
81% |
|
80% |
|
+1 p.p. |
|
92% |
|
94% |
|
-2 p.p. |
||||
|
Internal audits at stores increased 12%, in line with the 10% growth of the network in the year (from 1,290 stores in 2023 to 1,438). Follow-up audits are carried out by internal and external audit teams, depending on previous results and based on internal risk metrics and the frequency of incidents – priority corrective measures are, therefore, subsequently evaluated. The decrease reflects more positive results in initial audits, and therefore fewer control points to recheck.
At the distribution centres, the number of audits is explained by the results of previous assessments. The previous year’s performance level has decreased slightly due to changes in methodology. Standards have become stricter in what regards temperature control throughout the entire storage process, product dispatch and delivery to stores, as well as traceability systems.
Facility analyses
Poland
We carried out 14.3% fewer analyses than in 2023, reflecting the reduction of surfaces analysis (including work surfaces and utensils) and manipulators. This reduction is explained by a reassessment of the risk analysis of meat counters, that resulted in a lower frequency during the year, and the fact that there were less stores with juice squeezers (11 stores in 2024 versus 16 in 2023) and roasted chicken (28 stores in 2024 versus 38 in 2023), which contributed to the finished products category. The increase of water analyses is explained by the expansion of Biedronka network.
Number of analyses/samples collected in Poland |
|
2024 |
|
2023 |
|
Δ 2024/2023 |
---|---|---|---|---|---|---|
Work surfaces |
|
103,596 |
|
121,919 |
|
-15.0% |
Manipulators |
|
8,290 |
|
9,480 |
|
-12.6% |
Raw materials/Finished product |
|
205 |
|
334 |
|
-38.6% |
Water |
|
2,445 |
|
1,885 |
|
+29.7% |
Total |
|
114,536 |
|
133,618 |
|
-14.3% |
Portugal
A total of 124,906 food safety and quality analyses were carried out at Pingo Doce and Recheio stores, at distribution centres and other facilities (such as the fresh dough factory, kitchens and canteens), which represents a 9.6% increase compared to 2023. As regards work surfaces and manipulators, the increase is mainly related to the usual annual planning and the opening of Pingo Doce stores based on its new store concept “All About Food 2.0” that embodies the Company’s long-term vision for the business, based on the banner’s competitive advantages and key differentiating factors: Perishables, Private Brand and Meal Solutions.
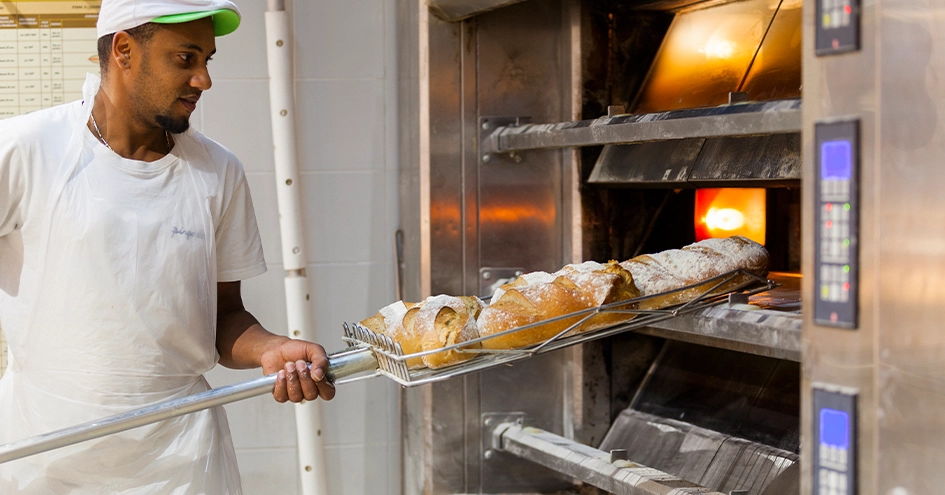
Number of analyses/samples collected in Portugal |
|
2024 |
|
2023 |
|
Δ 2024/2023 |
---|---|---|---|---|---|---|
Work surfaces |
|
61,003 |
|
51,461 |
|
+18.5% |
Manipulators |
|
19,928 |
|
19,867 |
|
+0.3% |
Raw materials/Finished product |
|
37,367 |
|
36,271 |
|
+3.0% |
Water |
|
6,608 |
|
6,407 |
|
+3.1% |
Total |
|
124,906 |
|
114,006 |
|
+9.6% |
Colombia
In 2024, the number of analyses carried out increased 14% compared to 2023, as a result of the expansion of the Ara network.
Number of analyses/samples collected in Colombia |
|
2024 |
|
2023 |
|
Δ 2024/2023 |
---|---|---|---|---|---|---|
Work surfaces |
|
2,793 |
|
2,284 |
|
+22.3% |
Manipulators |
|
2,589 |
|
2,285 |
|
+13.3% |
Raw materials/Finished product |
|
2,549 |
|
2,285 |
|
+11.6% |
Water |
|
5,478 |
|
4,883 |
|
+12.2% |
Total |
|
13,409 |
|
11,737 |
|
+14.2% |
Product analyses
The products we market are assessed as to their quality and safety at external, accredited laboratories. In total, 58,298 analyses of Private Brand food products were carried out (0.7% more than in 2023) and 20,879 on perishables (21.3% more).
Poland
Number of analyses/samples collected in Poland |
|
2024 |
|
2023 |
|
Δ 2024/2023 |
---|---|---|---|---|---|---|
Private Brand |
|
23,077 |
|
20,833 |
|
+10.8% |
Private Brand – Food |
|
21,750 |
|
19,606 |
|
+10.9% |
Private Brand – Non-food |
|
1,327 |
|
1,227 |
|
+8.1% |
Perishables |
|
8,611 |
|
6,402 |
|
+34.5% |
Fruit and vegetables |
|
4,182 |
|
4,018 |
|
+4.1% |
Meat and fish |
|
2,991 |
|
1,698 |
|
+76.1% |
Bakery |
|
976 |
|
218 |
|
+347.7% |
Eggs |
|
462 |
|
468 |
|
-1.3% |
Total |
|
28,540 |
|
27,235 |
|
+4.8% |
For the increase in the number of analyses of food and non-food products contributed Biedronka’s expansion, the establishment of more partnerships with suppliers and the broadening of regular and seasonal assortments, which affected the volume of products to be analysed.
In the meat and fish category, the increase is explained by the expansion of stores with meat counters and, consequently, the inclusion of a greater number of products in the annual regular analyses plan. Furthermore, the number of salmonella and food fraud prevention analyses in these categories were much higher than in 2023. For bakery, the growth is due to methodological changes in laboratory analyses. Also. fruit and vegetables suppliers and assortment were added during the year. For eggs, although a slight decrease was registered, the number of analyses was in line with audit planning and risk assessment.
Portugal
Number of analyses/samples collected in Portugal |
|
2024 |
|
2023 |
|
Δ 2024/2023 |
||||
---|---|---|---|---|---|---|---|---|---|---|
Private Brand |
|
22,486 |
|
22,639 |
|
-0.7% |
||||
Private Brand – Food1 |
|
18,494 |
|
17,795 |
|
+3.9% |
||||
Private Brand – Non-food |
|
3,992 |
|
4,844 |
|
-17.6% |
||||
Perishables |
|
11,909 |
|
10,546 |
|
+12.9% |
||||
Fruit and vegetables |
|
1,857 |
|
2,335 |
|
-20.5% |
||||
Meat |
|
689 |
|
1,224 |
|
-43.7% |
||||
Fish |
|
1,233 |
|
1,188 |
|
+3.8% |
||||
Bakery |
|
498 |
|
598 |
|
-16.7% |
||||
Meal Solutions |
|
7,632 |
|
5,201 |
|
+46.7% |
||||
Total |
|
34,395 |
|
33,185 |
|
+3.6% |
||||
|
The expansion of the Pingo Doce network and it’s “All About Food 2.0” concept was the main reason for the increase in the number of analyses. In the case of non-food products, there were some methodological changes during the year which explain the results:
- the transition of the pet food references to the food category;
- the reduction of samples collected when the same product is sold under two different Private Brands.
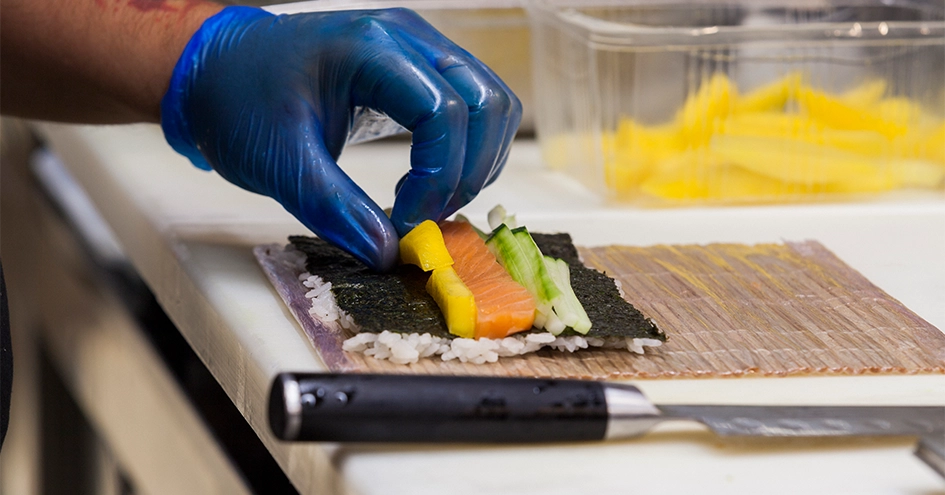
As regards perishables, the most significant increase was in the meal solutions category, which is assessing ways of extending the shelf-life of new/current products. For fruit and vegetables, meat and bakery, the risk assessment and compliance history in previous years, as well as close monitoring of upstream production, led to a reduced need for analyses.
Colombia
Number of analyses/samples collected in Colombia |
|
2024 |
|
2023 |
|
Δ 2024/2023 |
---|---|---|---|---|---|---|
Private Brand |
|
26,538 |
|
26,250 |
|
+1.1% |
Private Brand – Food |
|
21,202 |
|
20,516 |
|
+3.3% |
Private Brand – Non-food |
|
5,336 |
|
5,734 |
|
-6.9% |
Perishables |
|
363 |
|
260 |
|
+39.6% |
Fruit and vegetables |
|
152 |
|
100 |
|
+52.0% |
Meat |
|
123 |
|
142 |
|
-13.4% |
Fish |
|
35 |
|
8 |
|
+337.5% |
Bakery |
|
53 |
|
10 |
|
+430.0% |
Total |
|
26,901 |
|
26,510 |
|
+1.5% |
The increase in the analysis of Private Brand food products is in line with the expansion of the regular assortment (195 more products than in 2023), the expansion of the store network and the usual risk analysis. As in food articles, the non-food category had its sampling plan adjusted in its frequency.
In the case of perishables, the higher number of samples collected is due to adjustments in the risk assessment of suppliers and products, including analyses for food authenticity. It is also explained by the inclusion of products from the new perishable’s category. For the bakery category, shelf-life analyses were conducted to extend the display time of hot counter products like chicken pies. Analyses for new products that were launched also contributed to this increase.
Food recalls and withdrawals
With the aim of protecting public health and preserving the reputation and credibility of our Companies and brands, we do not hesitate in removing from market products that may pose a threat to consumers and society. Continuous monitoring, communication with the official health authorities, and the traceability of products and suppliers enable a fast and effective prevention of and/or reaction to any incidents.
There are two types of food product removal, which address specific risks to the health and safety of consumers:
- recall7 (removal from sale of products with potential health risks);
- withdrawal8 (removal from sale of products that do not pose a health risk).
In both cases, internal investigations are carried out and, if necessary, at suppliers, to identify the causes and implement the appropriate corrective measures for prevention.
The severity of the risks to consumer health and safety are classified as:
- Level I – critical (recall): aspects that may affect food safety and public health;
- Level II – food safety and quality (withdrawal): aspects that may affect the consumer experience and food safety of the product;
- Level III – labelling (withdrawal): aspects related to legal labelling requirements.
|
|
|
|
Level I |
|
Level II |
|
Level III |
|
Total incidents |
||||||||
---|---|---|---|---|---|---|---|---|---|---|---|---|---|---|---|---|---|---|
Food product recalls/withdrawals |
|
2024 |
|
2023 |
|
2024 |
|
2023 |
|
2024 |
|
2023 |
|
2024 |
|
2023 |
||
Group |
|
|
|
4 |
|
6 |
|
163 |
|
221 |
|
54 |
|
63 |
|
221 |
|
290 |
Portugal (Pingo Doce and Recheio) |
|
Private Brands |
|
0 |
|
0 |
|
75 |
|
63 |
|
22 |
|
16 |
|
97 |
|
79 |
|
Perishables |
|
1 |
|
0 |
|
37 |
|
57 |
|
13 |
|
30 |
|
51 |
|
87 |
|
Poland (Biedronka) |
|
Private Brands |
|
2 |
|
5 |
|
32 |
|
56 |
|
17 |
|
10 |
|
51 |
|
71 |
|
Perishables |
|
1 |
|
0 |
|
1 |
|
1 |
|
0 |
|
0 |
|
2 |
|
1 |
|
Colombia (Ara) |
|
Private Brands |
|
0 |
|
0 |
|
9 |
|
36 |
|
2 |
|
7 |
|
11 |
|
43 |
|
Perishables |
|
0 |
|
1 |
|
9 |
|
8 |
|
0 |
|
0 |
|
9 |
|
9 |
In 2024, 221 incidents leading to product removals were recorded, 23.8% less than in 2023. The vast majority of these (98.2%) were Level II and Level III, i.e. withdrawals, while recalls were only 1.8% (critical, Level I). In the last case, there is a decrease of 33.3% compared to 2023, a year in which there was already a 53.8% decrease compared to 2022. These numbers show a downward trend in this indicator.
None of the Level I recalls had causes attributable to Jerónimo Martins, the main causes being requests from authorities and suppliers. To prevent nonconformities, and the need for withdrawals/recalls, we control and monitor suppliers and products, including in what regards the implementation of action plans, maintenance and packaging changes. Corrective actions are monitored to minimise the risk to consumers’ health and to enable the marketing of products to be resumed.
Food quality and safety internal training
Offering high quality and safe food products encompasses not only supporting and monitoring our supply chain, but also the permanent investment in professional teams that fully embed the competences needed to provide a skilled service to our consumers.
This investment follows the expansion of our activities in all countries, which has resulted in more employees being prepared for the daily work. The figures have therefore increased globally in our operations: the number of people trained in food safety and hygiene grew by 14.8% compared to the previous year as well as the training courses (17.4%). Therefore, the training volume increased 2.6%.
|
|
Training volume1 |
|
Training courses |
|
Employees trained |
||||||||||||
---|---|---|---|---|---|---|---|---|---|---|---|---|---|---|---|---|---|---|
Food safety and hygiene training |
|
2024 |
|
2023 |
|
2024 |
|
2023 |
|
2024 |
|
2023 |
||||||
Group |
|
249,346 |
|
242,940 |
|
9,727 |
|
8,285 |
|
57,130 |
|
49,772 |
||||||
Portugal2 |
|
60,328 |
|
37,548 |
|
3,592 |
|
3,426 |
|
11,120 |
|
9,597 |
||||||
Poland (Biedronka) |
|
27,731 |
|
25,454 |
|
6,048 |
|
4,786 |
|
25,135 |
|
21,926 |
||||||
Colombia (Ara) |
|
161,287 |
|
179,938 |
|
87 |
|
73 |
|
20,875 |
|
18,249 |
||||||
|
Training in Poland reached 25,135 employees, 14.6% more than in 2023, due to the network expansion and more training initiatives, thus resulting in a 9% growth in training volume. Some of the topics covered in Biedronka included: food safety systems (e.g., international HACCP standards), waste separation for recycling, washing and cleaning activities (to ensure good food production) and hygiene practices.
Training volume hours in Portugal rose by 60.7% in comparison to 2023, the most significant increase in all three countries. This was primarily driven by the renewal of the meat handlers card training which is required every three years. Other training courses included requirements associated with the food safety management system, under the international HACCP risk control standard and food defence practices.
In Colombia, though there were more initiatives and people trained, there was a decrease in the training volume due to the reduction in some courses’ duration. The most significant example is the content of “Tiendas Siempre Limpias” (Stores Always Cleaned), whose duration was halved. The training covered topics such as in-store hygiene plan, water control and waste handling, quality audits and control visits, cold chain and critical control points.
Partnerships and support
We continued to hold regular talks with public and private benchmark institutions in the countries where we do business to learn and share knowledge about food, nutrition and health9.
For several years, we have been a member of The Consumer Goods Forum and its Global Food Safety Initiative10, a coalition of action that gathers retailers and manufacturers from around the world. We are also present in the Global G.A.P. (Good Agricultural Practices), an organization that sets standards for safe and responsible farming regarding crop production, animal welfare, worker’s welfare, traceability, among others. We are the only retailer with the head office in Portugal represented in its International Fruit and Vegetables Committee11.
Pingo Doce is an active member of APED (the Portuguese Association of Distribution Companies) and participates in technical committees, including those dedicated to food quality. The Company has several long-standing partnerships with organisations that aim to contribute to healthy eating as a pillar of public health, such as the Portuguese Directorate-General for Health within the framework of the National Programme for the Promotion of Healthy Eating, the Portuguese Coeliac Association and the Portuguese Nutrition Association (Pingo Doce sponsored the XXIII Congress of Food and Nutrition in 2024).
Pingo Doce also collaborates with academia, namely with the University of Lisbon’s Instituto Superior Técnico (School of Engineering and Technology) and the Instituto Nacional de Saúde Doutor Ricardo Jorge (Ricardo Jorge National Health Institute).
In 2024, and for the second time, Biedronka was the main partner and sponsor of the Health Olympiad, developed with the Polish Red Cross. The competition is intended for students from primary schools to high schools. At each stage of the competition, participants complete a knowledge test covering issues related to healthy lifestyle, balanced nutrition, physical activity, ecology, and fighting food waste. The competition registered 16,348 participants from 1,150 primary and secondary schools.
In 2024 Ara maintained its participation in the ICONTEC (the national certification body of Colombia) technical committee groups, dedicated to fresh fruits and vegetables, fishing and aquaculture. The Company has also participated in the Colombia Productiva’s12 working groups alongside its strategic partners focusing on quality and safety of bakery products finalized at stores and meat.
1 The Hazard Analysis and Critical Control Points (HACCP) system is designed to prevent potential risks that cause harm to consumers, by eliminating or reducing hazards and thereby ensuring food is safe for consumption.
2 A set of international standards aimed at promoting food safety and consumer protection. The Codex Alimentarius is available here.
3 There were 1,323 counters in 2024, 244 more than in 2023. In Poland, internal audits, including follow-up audits, of stores are outsourced to independent entities such as Diversey, Det Norske Veritas (DNV-GL), and Lloyd’s Register.
4 Implemented in 2021, this operation consists of micro-fulfilment centres (MFC) operated by employees to handle orders placed by consumers through the Glovo fast distribution partner application. By the end of 2024 Biedronka covered 23 locations (versus 18 in 2023) in the cities of Warsaw, Łódź, Krakow, Gdańsk, Poznań, Wrocław, Lublin, Bydgoszcz and Olsztyn. More information is available in “Focus on profitable growth”.
5 In 2024, 486 stores offered an organic bread range (versus 489 in 2023). External controls relating to organic certification were carried out by BioCert, an independent entity duly authorised by official bodies for such purpose.
6 At the distribution centres, internal audits are carried out by food safety and quality technicians, while external audits, within the scope of ISO22000 certification, are carried out by Lloyd’s Register.
7 Recall: a mandatory action taken by the Group’s Companies in response to inspections carried out by local authorities, the results of laboratory analyses or internal audits, or complaints/reports (from producers, retailers, government agencies, or consumers). Notices are published using the appropriate medium for consumers to return or destroy the product concerned.
8 Withdrawal: a voluntary or mandatory action that can be taken on two occasions based on the risk analysis of the Companies or inspection by a local authority: (a) when quality defects (e.g. colour or texture), weight defects or irregularities are detected in the labelling (which does not pose a potential risk to the health or safety of consumers); or (b) as a precaution pending investigation into a potential risk to health and safety. If a credible risk is identified, the product is removed from sale and it is categorised as a recall.
9 More details about partnerships can be found on our website.
10 More details here
11 To know more visit Fruit and Vegetables Technical Committee
12 This organization was created by the Ministry of Commerce, Industry and Tourism in 2008 with the aim of promoting competitiveness in the industry while supporting Colombian companies to improve indicators in production processes such as quality, human capital and productivity.